SERVICES
EBP Processing flow
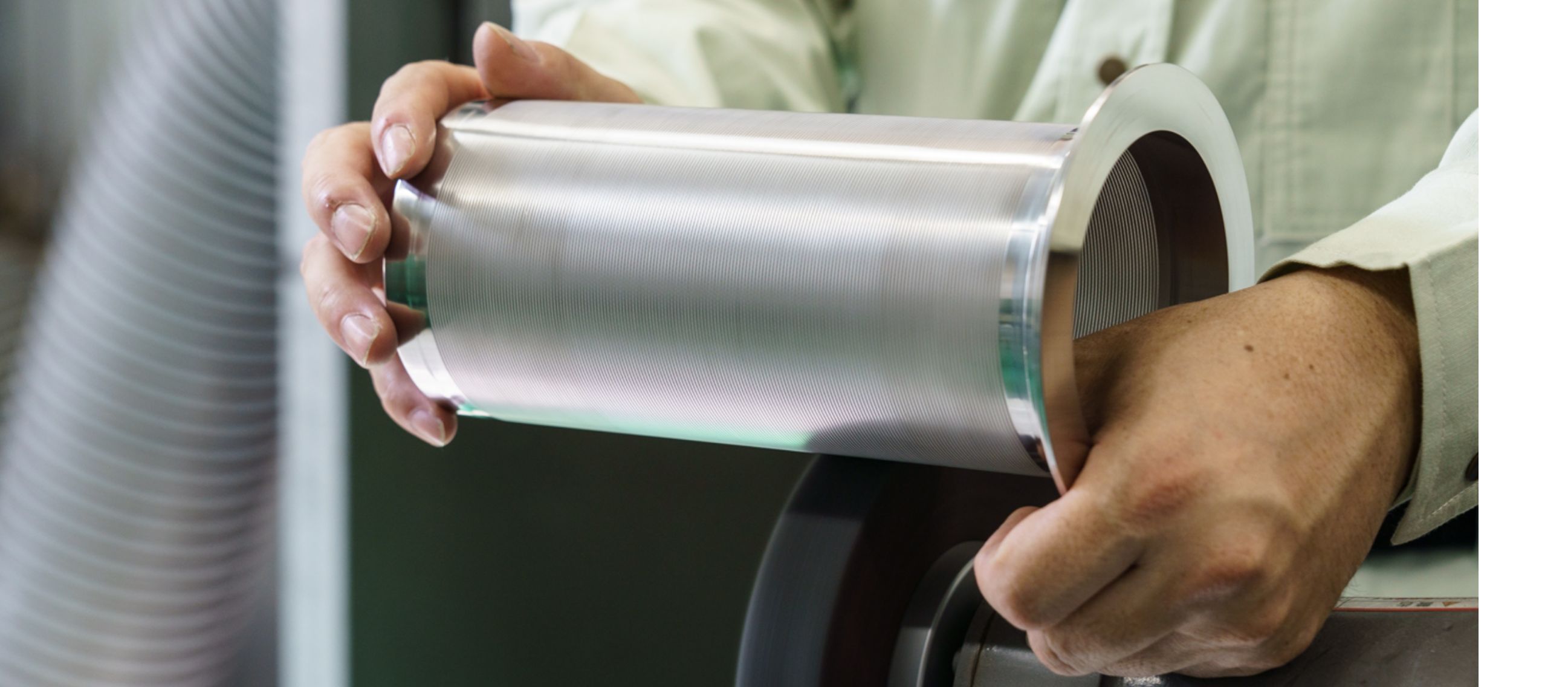
EBP Processing flow
01〜04 Duration: about 3-4Weeks
01
Material Preparation
- Sheet rolling process
- Stainless steel sheet is joined at both ends by TIG welding or spot welding, and then formed into rolls.
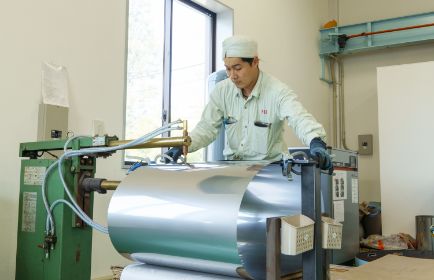
02
Preprocessing
- Degreasing
- Degreasing and cleaning the cylindrical stainless steel sheet to remove oil and dust (dirt) so that it does not affect the drilling process.
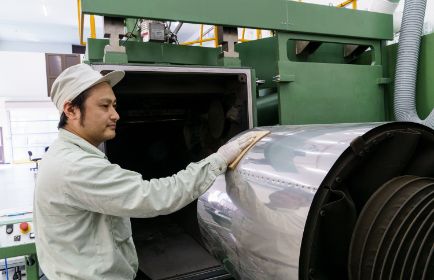
03
Hole drilling
- Hole drilling
- Cylindrical stainless steel sheet is drilled using an electron beam drilling machine.
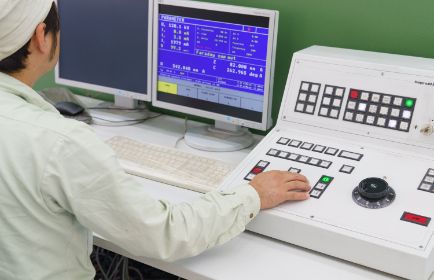
04
Post processing
- Pickling and deburring (primary removal)
- Acid cleaning and mechanical primary removal of dirt after drilling.
- Dimensional cut
- After primary removal of burrs, the cylindrical stainless steel sheet is returned to its flat form and cut to the appropriate dimensions.
- Deburring (secondary removal)
- Remove the burrs on the back and in the hole by pickling.
- Cleaning
- Remove oil, grease, and other contaminants with an organic solvent.
- Midterm inspection
-
- Make sure there are no distortions, scratches, or bends.
- According to the production drawing, inspect the hole diameter, pitch and thickness.
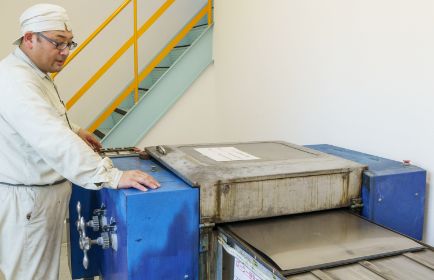
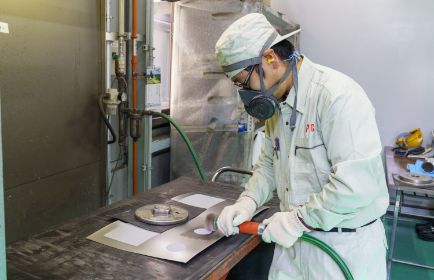
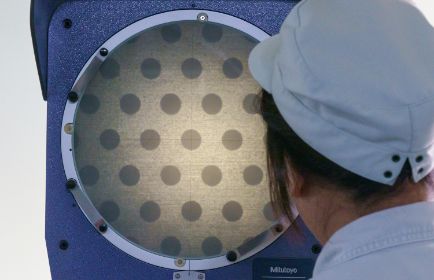
Structure of the processing machine
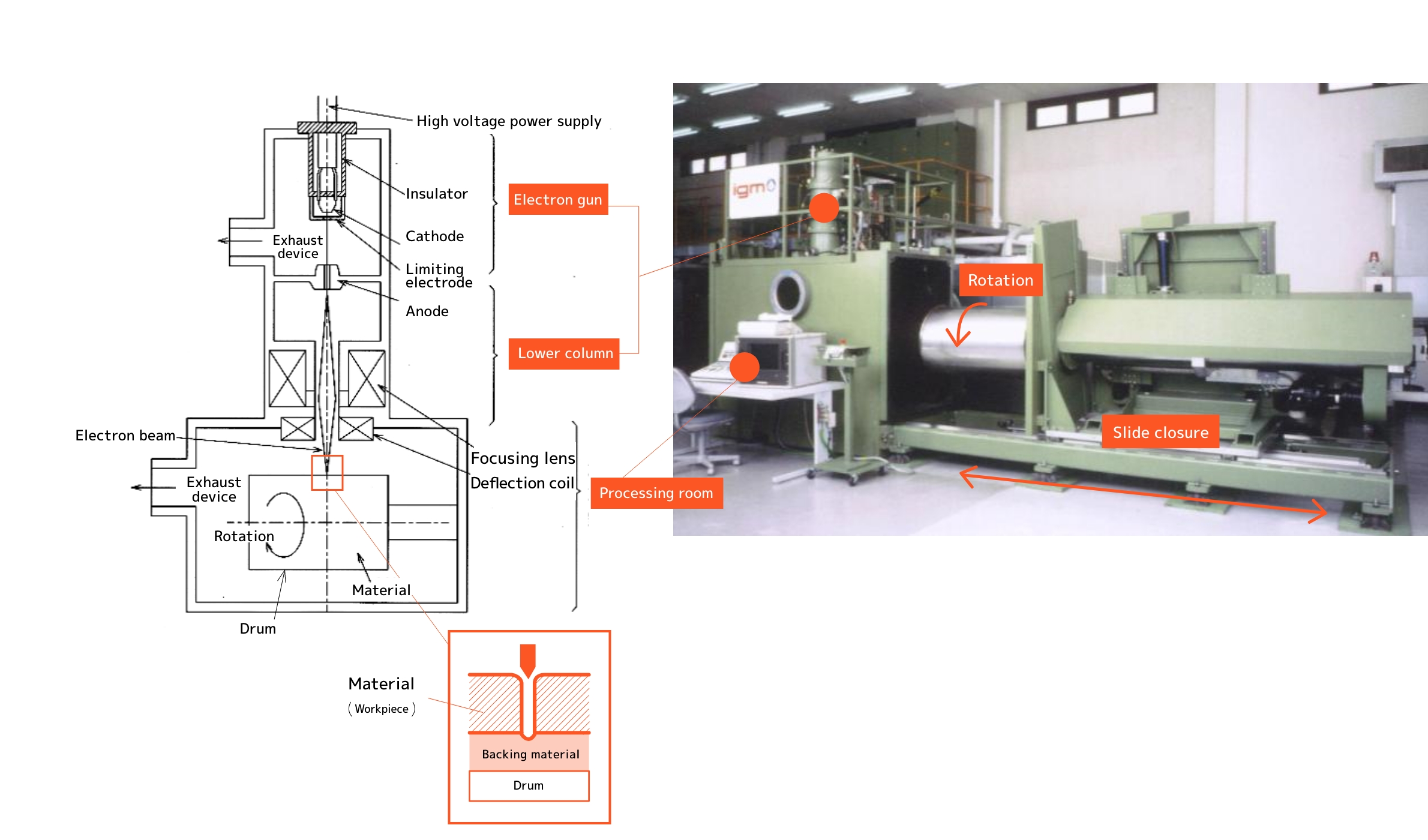
A vacuum is created in the processing room to prevent beam divergence, improve insulation, and prevent oxidation.
Continuous processing is possible by irradiating the electron beam in pulses at high speed while the drum is rotating.
05〜06 Duration: about 3Weeks
05
Molding
(secondary processing)
(secondary processing)
- Cutting / Cylindrical forming / Welding assembly
-
- Cut the screen plate according to the fabrication drawing.
- After cutting to a predetermined size, the cylinder is formed and the ends are joined.
- Cylindrically formed screens and machined parts such as flanges are joined under optimized welding conditions.
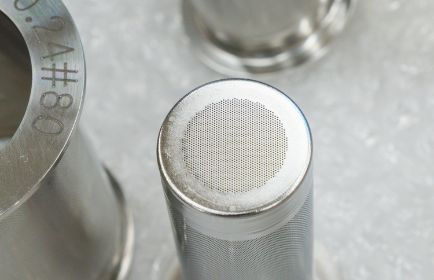
06
Surface treatment
- Electropolishing
- Electropolishing is applied for the purpose of final cleaning.
07
Inspection
- Final inspection
-
- Make sure that there are no distortions, scratches or bends in the entire product area.
- Check that there is no blockage of the hole by foreign objects in the entire drilling area of the screen section.
- Dimensional inspection of major dimensions according to the production drawing.
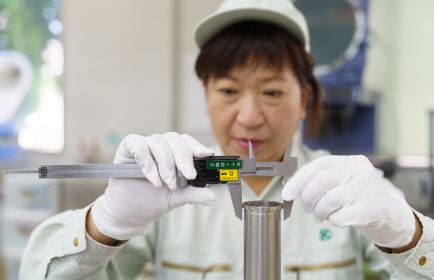
Drilling Process
01 Irridiation
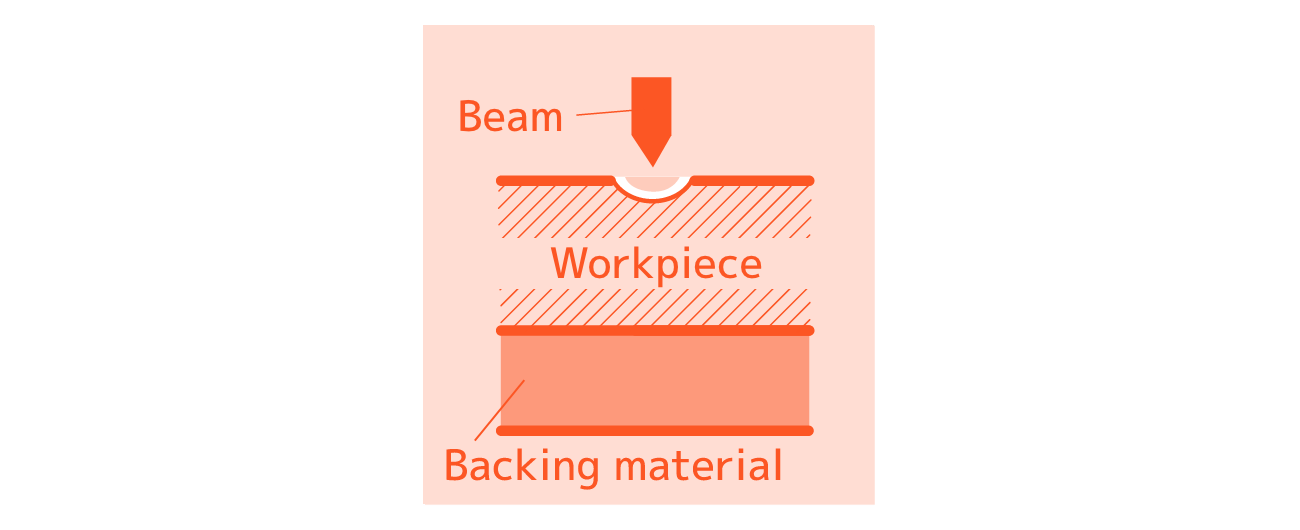
The focused electron beam irradiates the workpiece and first melts a portion of it.
02 Penetration
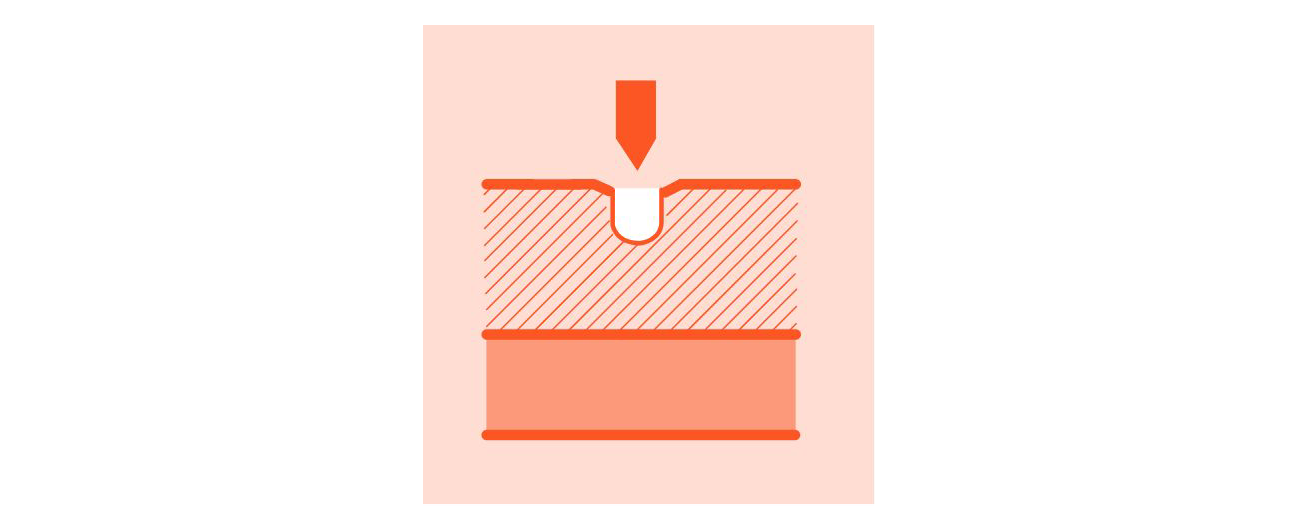
The cavity filled with evaporated material deepens, and a molten layer forms around it.
03 Perforation
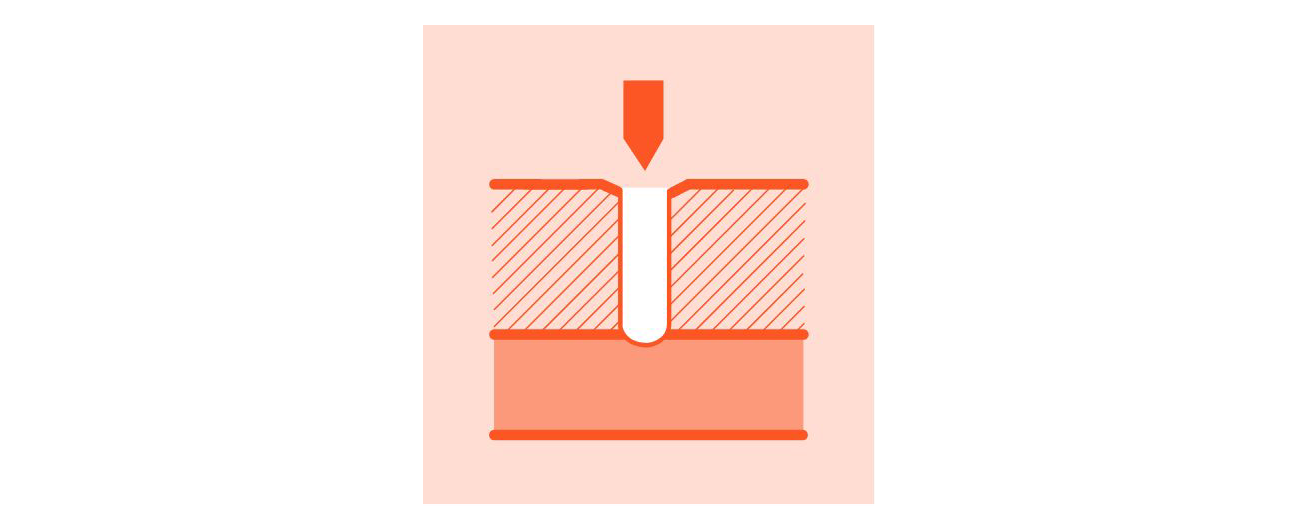
The electron beam pierces the workpiece and reaches the backing material.
04 Dispersion
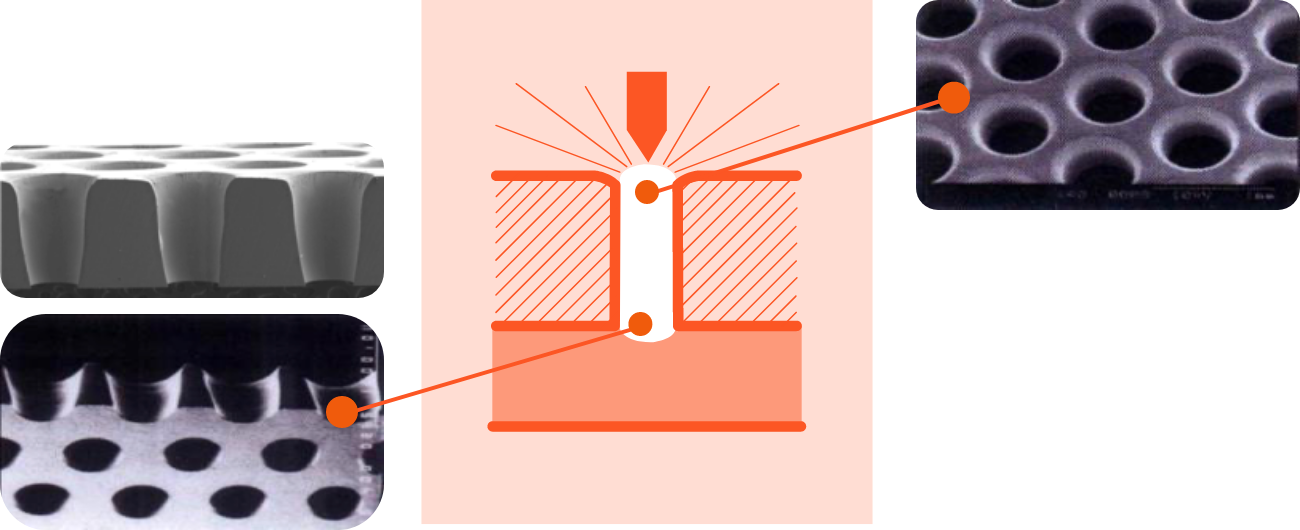
The high vapor pressure of the backing material disperses the molten metal remaining inside the through hole to the outside, completing the drilling.